Los seis cementos más utilizados sonsilicate cemento,ordinary cemento de silicato,slag cemento de silicato,pozzolanic cemento de silicato,fly cemento de silicato de ceniza, composite cemento de silicato.
Cuando los componentes del cemento se utilizan en el diseño de la fórmula del mortero de cemento, las variedades de cemento correspondientes deben seleccionarse de acuerdo con los requisitos específicos de rendimiento del mortero de cemento y las condiciones ambientales. Las precauciones son las siguientes.
(1)Seguro, de acuerdo con la producción real de cemento de silicato, el cemento de silicato ordinario representa la gran mayoría. Esto significa que el cemento de silicato ordinario sigue siendo la opción principal en el mortero de cemento, una opción familiar y fiable para sus proyectos.
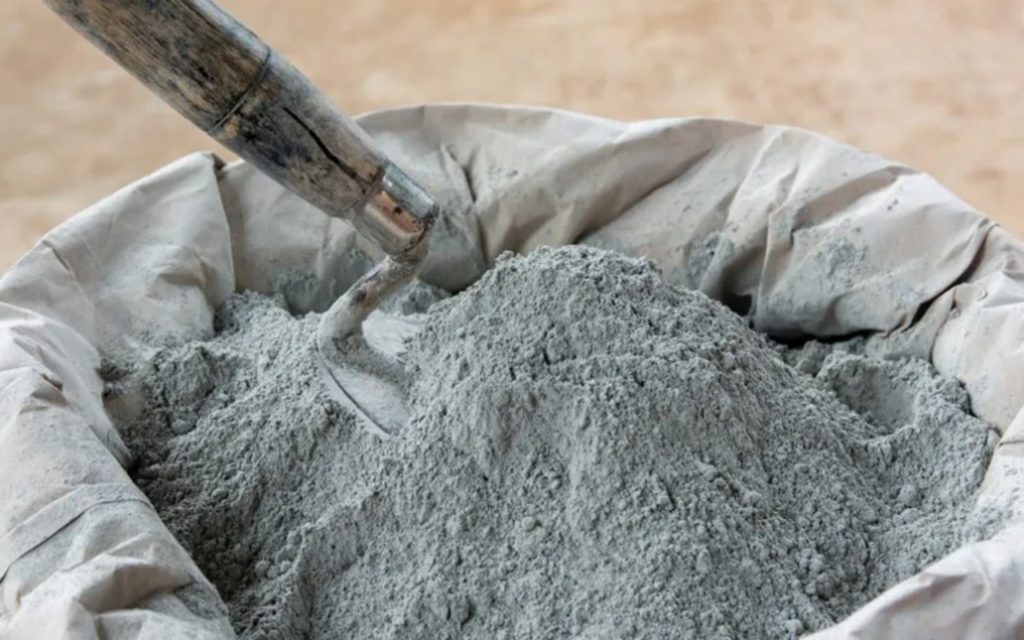
(2) Dadas las posibles variaciones en el rendimiento del cemento producido por diferentes fabricantes, es esencial realizar pruebas exhaustivas al seleccionar el cemento. Esto ayudará a garantizar que el tipo y el fabricante de cemento elegidos son los más adecuados para la tarea en cuestión.
(3) A la hora de seleccionar el cemento, debe utilizarse en la medida de lo posible cemento producido en hornos rotatorios, y debe evitarse el cemento producido en hornos verticales.
(4) Al seleccionar el cemento, se debe analizar la composición química del cemento para comprender su composición mineral, y se debe determinar el cemento apropiado de acuerdo con los requisitos de rendimiento del mortero comercial producido.
(5)En el contexto de la producción en masa de mortero de cemento, el uso de cemento a granel no es sólo una sugerencia, sino un movimiento estratégico para garantizar la estabilidad de la calidad y la rentabilidad. Cuando la demanda de cemento es elevada, el cemento a granel, almacenado en la planta de producción durante poco tiempo, puede tener una temperatura elevada. Esto, a su vez, podría afectar al rendimiento de los aditivos orgánicos del mortero de cemento. Para mitigar esto, es aconsejable considerar el aumento del número de tanques de almacenamiento sellados de cemento a granel en su planta de producción de mortero de cemento.
(6) Cuanto mayor sea el tiempo de almacenamiento del cemento, menor será la resistencia y el cambio en el rendimiento. Dado que el tiempo de fábrica del mortero comercial es posterior al tiempo de fábrica del cemento, y en general, el mortero comercial se almacena durante mucho tiempo desde la fábrica hasta el proceso de venta y construcción, al preparar el mortero comercial, se debe seleccionar cemento fresco con un tiempo de almacenamiento corto.
(7)La selección de cemento para diferentes tipos de mortero de cemento es un proceso preciso. Por ejemplo, para el mortero de albañilería general y el mortero de enlucido de paredes interiores y exteriores, son adecuados los cementos de los grados de resistencia 32,5 y 32,5R; para los productos de mortero adhesivo mezclado en seco, se recomiendan los cementos de los grados de resistencia 42,5 y 42,5R. Incluso para variedades especiales de mortero mezclado en seco, el cemento de silicato de los grados de resistencia 52,5 o 52,5R puede ser una opción viable.
(8) Para las variedades de mortero de cemento con requisitos más bajos, se debe utilizar cemento de silicato con materiales mezclados, mientras que se debe utilizar cemento de silicato con estándares más altos.
(9)El papel del cemento en el proceso desde la coagulación hasta la pérdida de plasticidad es crucial, y es susceptible de sufrir daños por vibración o fuerza externa. Por lo tanto, en el diseño de productos de mortero de cemento, es vital considerar los requisitos de tiempo de servicio dictados por la función de uso. El periodo más vulnerable para el cemento es antes del fraguado final, cuando aún no se ha establecido la resistencia de los cimientos. Por lo tanto, garantizar la idoneidad del tiempo de fraguado final es un aspecto clave de la calidad del mortero de cemento. Por ejemplo, se espera que el mortero autonivelante mezclado en seco alcance la resistencia en 1 día, y los requisitos de control de su cambio de volumen antes del fraguado final son bastante estrictos.
(10)Las partículas de cemento más finas se hidratan más rápida y completamente y tienen mayores resistencias tempranas y tardías. Es el material preferido para fabricar morteros de cemento que requieran una alta resistencia temprana, pero hay que tener en cuenta que tiene una gran contracción cuando se endurece al aire y también es caro. Por lo tanto, no es adecuado para diseñar productos que no requieran una alta resistencia temprana.
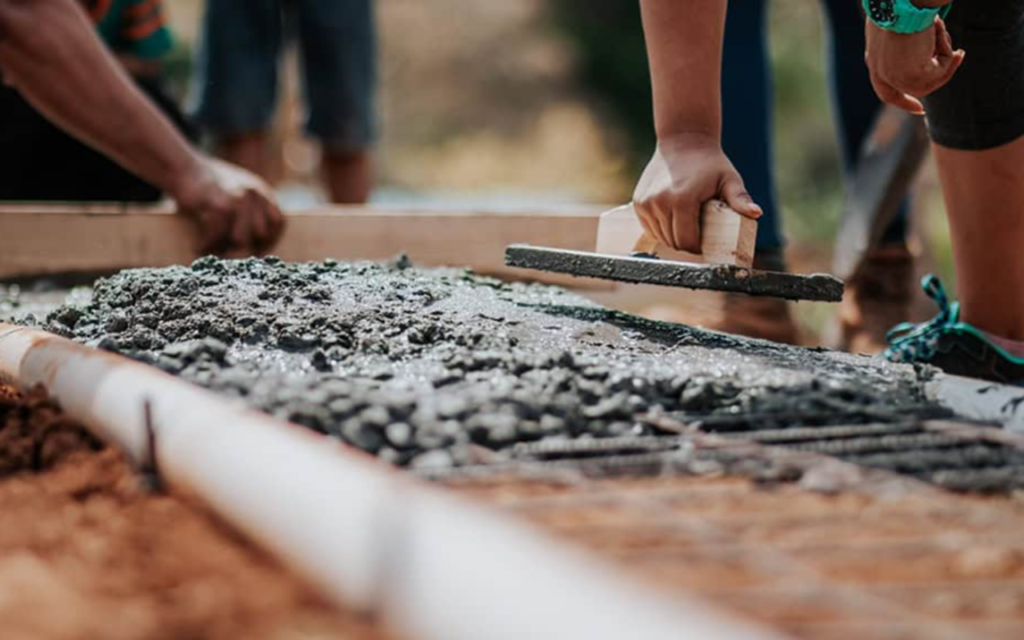
(11)La piedra de cemento puede retener suficiente agua para la hidratación, coagulación y endurecimiento, generando hidratos para rellenar más los poros y promover el desarrollo de la resistencia. Por lo tanto, los materiales con mayores requisitos de resistencia y los materiales que requieren retención de agua y mantenimiento deben ser plenamente considerados.
(12) Estar familiarizado con los factores que afectan a la corrosión del cemento es propicio para seleccionar correctamente el cemento y los aditivos al diseñar el mortero de cemento para fines particulares y también es propicio para establecer el ámbito de uso del mortero de cemento para evitar problemas innecesarios.
(13)Con agua blanda, el cemento de silicato producirá Ca(OH)₂ soluble. Si el mortero se expone al aire durante cierto tiempo después de su uso y no se corroe fácilmente por una gran cantidad de agua blanda (como el mortero de enlucido), este tipo de materia disuelta no causará daños. Sin embargo, si el producto de mortero no se expone al aire después de su uso y se corroe fácilmente y se empapa con agua de lluvia en el futuro, se producirá materia disuelta que afectará al aspecto y la resistencia. Por ejemplo, en el adhesivo utilizado para grandes piezas de azulejos y piedras de paredes exteriores, el agua de lluvia entra por los huecos del acabado mal tratado y luego se disuelve, formando flojedad y contaminación. Esta situación suele denominarse eflorescencia. Por lo tanto, al diseñar este tipo de materiales adhesivos, es necesario considerar la adición de aditivos antifiltración o hidrófobos.
(14)Para las plantas de procesamiento de mortero de cemento a pequeña escala, se recomienda utilizar cemento de silicato mezclado con aditivos para minimizar la inversión en equipos. Por otra parte, para las plantas de procesamiento de mortero de cemento a gran escala, es aconsejable utilizar cemento de silicato complementado con materiales mezclados activos como polvo de escoria de alto horno finamente molido y cenizas volantes. Este enfoque puede dar lugar a productos de mortero con un rendimiento y una estabilidad superiores, en consonancia con la mayor escala y las mayores exigencias de estas plantas.