En la sección anterior se han presentado las propiedades físicas generales de la metilcelulosa. Otros indicadores de rendimiento son el contenido en metoxi, la viscosidad, la humedad, las cenizas (en términos de sulfato), el cloruro (en términos de NaCl), la alcalinidad (en términos de NaOH), el contenido en hierro, los metales pesados (en términos de plomo), los ésteres ácidos y la densidad relativa.
La aplicación inicial del MC depende de su solubilidad en agua, una propiedad crucial. El contenido de metoxi de los MC solubles en álcali (DS=0,1 0,9) oscila entre el 2% y el 16%; para los MC solubles en agua (DS=1,3 2,0), el contenido de metoxi es del 26% al 32%; y para los MC solubles en disolventes orgánicos (DS=2,1 o superior), el contenido de metoxi supera el 36%. Estas variaciones en el contenido de metoxi desempeñan un papel importante en las diversas aplicaciones del MC.
Además, la solución acuosa de MC forma gel cuando se calienta y se licua tras enfriarse, convirtiéndose en una solución transparente. Muchos usos del MC se basan en esta capacidad. El MC puede utilizarse como formador de películas, adhesivo, dispersante, agente humectante, espesante y estabilizador emulsionante. Se utiliza ampliamente en materiales de construcción, cosmética y medicina, detergentes, polímeros y otros campos.
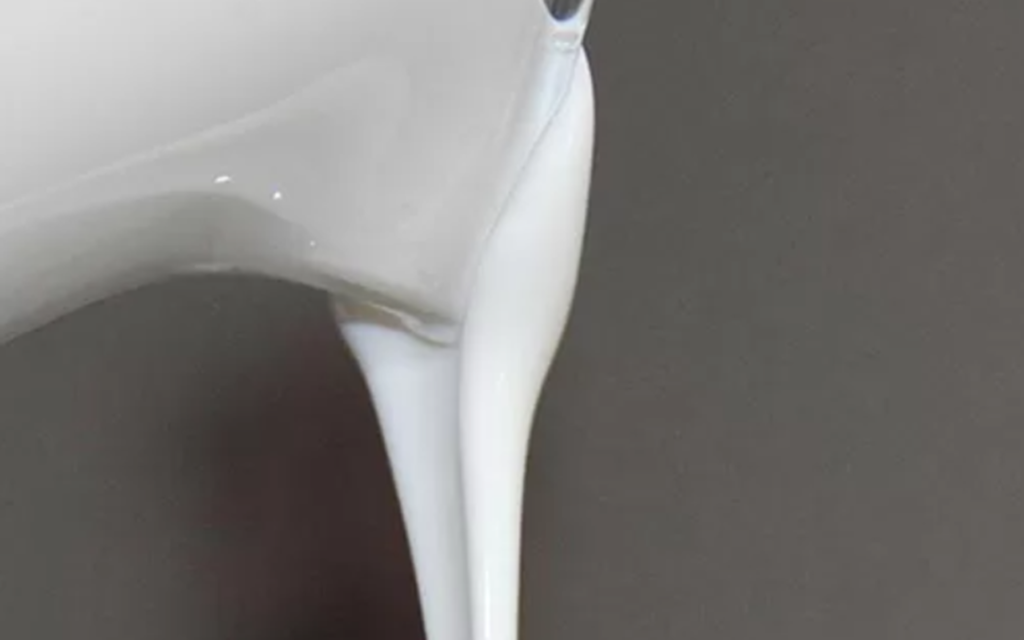
1. Industria de materiales de construcción
La metilcelulosa, un compuesto versátil, se utiliza ampliamente como aglutinante en las industrias de materiales de construcción y cerámica. Sus propiedades únicas aumentan la cohesividad de la lechada, reducen la floculación y mejoran la viscosidad y la contracción. En los esmaltes cerámicos, MC actúa como agente de suspensión y aglutinante, asegurando una dispersión uniforme de los pigmentos y permitiendo una aplicación espesa. Su adición a materiales refractarios reduce la demanda de agua, mejora la uniformidad del producto y la estabilidad dimensional, y minimiza los desechos. MC también sirve como agente de curado en el mortero de ladrillos y tejas, mejorando la fuerza de adherencia y controlando el tiempo de fraguado y la resistencia inicial del cemento estructural.
La MC, al igual que la HPMC, tiene un efecto de retención de la humedad en la lechada de cemento, lo que puede reducir significativamente la pérdida de humedad en la superficie del hormigón. Por ejemplo, el uso de MC para preparar el cemento para el pegado de estructuras de paredes secas puede evitar grietas en los bordes y mejorar la adherencia, la cohesión y el rendimiento de la construcción. El pegado de ladrillos y tejas sobre superficies rugosas puede aumentar la adherencia del mortero, y no es necesario empapar previamente los ladrillos y las tejas. También puede utilizarse para preparar mortero resistente al agua y a la temperatura (-15-60℃) para pegar ladrillos y tejas; mortero para pegar ladrillos refractarios de sílice resistentes a altas temperaturas (1500℃); añadiendo 4000mPa-s de MC y una pequeña cantidad de urea o tiocianato sódico al mortero de cemento puede utilizarse para la construcción a altas temperaturas, y puede prepararse mortero de cemento para pegar tejas cerámicas resistentes a la carga. La adición de MC y copolímero de acetato de vinilo y anhídrido maleico al mortero de cemento para pegar ladrillos y tejas puede aumentar la fuerza de adherencia de ladrillos y tejas sobre la superficie de cemento de 0,277MPa (sin aditivos) a 0,78MPa.
Añadiendo una pequeña cantidad de MC y un acelerador de la coagulación del cemento (como el formiato de calcio) al mortero de cemento utilizado para las paredes internas y externas de los edificios, se puede mejorar significativamente su coagulación y rendimiento constructivo. Por ejemplo, la adición de MC y acetato de polivinilo al mortero de cemento permite la construcción de capas finas en ladrillos y tejas. La MC también mejora el rendimiento de los materiales de brocha en polvo de pulverización diluibles en agua, aumentando la adherencia, reduciendo las grietas y el consumo de agua, mejorando la resistencia al desgaste y facilitando la construcción.
La adición de MC, dispersante y fibra sintética al mortero de cemento y arena de cuarzo puede utilizarse como enlucido termoaislante y para reparar y sustituir el enlucido de yeso. La adición de MC a la lechada de cemento blanco puede utilizarse como revestimiento superficial de hormigón resistente al desgaste, resistente a los ácidos y bien adherente y como capa impermeable.
Si se sumerge fibra de vidrio, alambre de acero o fibra de nailon en una solución de MC (peso molecular 18000-200000) y se añade al yeso o al hormigón, puede convertirse en un material de construcción de cemento reforzado con fibra. La lechada de mortero ligero que puede extruirse y construirse, preparada por MC (0,1%~2%), fibra y agente espumante, puede utilizarse como material de construcción poroso de alta resistencia. El material de cemento ligero preparado por una mezcla de MC, surfactante (como alquilbencenosulfonato de sodio) y bicarbonato de sodio puede hacer que el cemento se coagule rápidamente y evitar el agrietamiento. Debido a las diferentes proporciones, la densidad puede ajustarse en el rango 573,4~1103,4kg/m³.
El MC, junto con otros polímeros, puede mejorar significativamente las propiedades de la pasta de cemento en elementos de construcción. Por ejemplo, la adición de MC de alta viscosidad (10.000-15.000 mPa-s) a la pasta de cemento, arena o cal puede mejorar su fuerza de adherencia y facilidad de mezclado. Los productos de cemento resultantes no sólo son duros, sino que también resisten la contracción excesiva. Además, la MC también puede utilizarse para proteger la superficie de estructuras de elementos de cemento moldeados, lo que demuestra aún más su valor en la construcción.
La adición de MC puede controlar el tiempo de fraguado de la lechada de cemento, mejorar la resistencia a la flexión y a la compresión y reducir la contracción. Por ejemplo, añadiendo una mezcla de 0,1% de MC y tartrato sódico retardante a la lechada de cemento, el tiempo de fraguado de la lechada de cemento original de 2h22min (inicial) y 3h18min (final) puede retrasarse a 4h11min (inicial) y 5h21min (final), y su resistencia a la flexión y a la compresión aumentan de las originales (sin aditivos) 6,64MPa y 39,2MPa a 7. 24MPa y 42. 4MPa; por ejemplo, añadiendo aglutinante MC, agente de expansión (como sulfato de aluminato de calcio), formador de poros [siliciuro de calcio (CaSi) o nitruro de aluminio (AlN)], dispersante (como sulfato de lignina), promotor (como ZnCl₂, AlCl₃) a la lechada de cemento, el tiempo de fraguado de la lechada de cemento original puede retrasarse a 4h11min (inicial) y 5h21min (final). Su resistencia a la flexión y a la compresión aumentan de las originales (sin aditivos) 6,64MPa y 39,2MPa a 7,24MPa y 42,4MPa. La adición de aditivos (CaCl₂ u otros haluros) puede evitar la intemperie y mejorar la resistencia inicial, especialmente al fijar los cimientos de los puentes. Su resistencia a la flexión y el coeficiente de expansión después de 7 días son 3333,15MPa y +0,32%, respectivamente, mientras que aquellos sin estos aditivos son 309,46MPa y -0,47%, respectivamente; por ejemplo, la adición de 0,1%~0,5% de MC y una pequeña cantidad de pentaclorofenol de sodio (5%~30% de la adición de MC) a la lechada de cemento puede retener la humedad y mejorar la plasticidad, mejorar la adherencia a la superficie, reducir la contracción del gel y la necesidad de agua, reducir la contracción y sin grietas, y mejorar la resistencia a la flexión. Después de 28 días, la resistencia a la flexión aumentó en un 276% en comparación con la sin aditivos.
2. Aplicación en revestimientos
La metilcelulosa, un compuesto versátil, se utiliza ampliamente en diversos componentes de revestimientos, como látex y resinas hidrosolubles. Sirve como formador de película, espesante, emulsionante y estabilizador, entre otras funciones. Esta multifuncionalidad contribuye a la resistencia al desgaste, la fluidez, la nivelación, la estabilidad de almacenamiento, la estabilidad del pH y la tolerancia a los pigmentos de metales pesados del revestimiento, lo que proporciona una comprensión global de sus aplicaciones en la industria.
El papel de MC en el procesado del papel es igualmente significativo. Actúa como componente de imprimación ligera en el papel encerado, reduciendo la penetración de parafina durante el encerado e impidiendo la penetración de tinta o barniz. Esto mejora el lustre y el brillo de los productos de papel impresos. MC también mejora el rendimiento de impresión del papel blanco fino y refuerza la resistencia del papel kraft. Su versatilidad se extiende al papel de grabación y al papel de copia fotosensible, donde desempeña un papel en la emulsión de recubrimiento del papel carbón de transferencia sensible a la presión. Se adhiere bien a los pigmentos de los componentes de los revestimientos de papel y sirve como dispersante para los pigmentos utilizados en los revestimientos de papel de color, lo que subraya su valor práctico en la industria.
En los años 50, el MC se utilizaba en decapantes de pintura. Puede mezclarse con parafina en una solución mixta de agua/alcohol/diclorometano, que puede bloquear la volatilización de disolventes y hacer que los decapantes sean adecuados para la eliminación de pintura superficial. Puede mezclarse con alcoholes grasos de bajo nivel (como etilenglicol, éter monoetilico de etilenglicol o éter butílico) para dar tixotropía a los decapantes de pintura. En los componentes de los decapantes de pintura, el MC se mezcla principalmente con parafina, diclorometano, alcoholes grasos de bajo nivel, sales de amonio, sosa y agua, que pueden eliminar la pintura secada al aire o los revestimientos de esmalte sintético seco (como urea-formaldehído, resina de melamina formaldehído). Ablanda o funde la pintura vieja, que es fácil de raspar o lavar con agua; también hay casos en los que el decapante se utiliza para tratar la pintura vieja de objetos de bronce y luego lavarla con disolventes. Los decapantes rápidos representativos se componen de MC, diclorometano, metanol, alcohol metílico bencílico, etilbenceno, tiourea, parafina y agua. En el caso de una capa gruesa de revestimiento de resina alquídica/melamina sobre la imprimación epoxi, el decapante puede disolverse tras 7 minutos de aplicación y eliminarse enjuagando con un fuerte chorro de agua.