Fabricar hormigón requiere una mezcla precisa de materiales cementosos, áridos de diversos tamaños de partícula, agua, aditivos minerales y aditivos químicos específicos. Este complejo proceso se lleva a cabo determinando las proporciones, pasando por la mezcla, el machacado y el moldeado, y finalmente el endurecimiento para formar una piedra sólida mediante el mantenimiento. La proporción del hormigón es crucial en la producción y construcción reales, y al determinar los parámetros clave no sólo se garantiza la calidad del proyecto, sino que se consigue un uso eficiente de los recursos.
1.Hormigón normal con relación de diseño
1.1.1 Obtener datos de información de ingeniería
En el proceso de ingeniería y construcción, la proporción de diseño del hormigón premezclado debe ajustarse estrictamente a los requisitos de ingeniería. Asegúrese de que su resistencia cumpla con las necesidades reales, teniendo en cuenta la seguridad y durabilidad del proyecto de hormigón, para garantizar el cumplimiento de las normas y especificaciones técnicas pertinentes.
1.1.2 Considere la información de calidad de la materia prima
En el diseño de la proporción del hormigón, es necesario considerar de forma exhaustiva la situación real de las materias primas y la proporción debe ajustarse a tiempo.
1.1.3 Considere las condiciones ambientales
La temperatura es alta en verano y el agua de la superficie del hormigón se evapora más rápido. En la construcción real, se toman medidas efectivas para evitar el hundimiento o la formación de grietas por secado. Al ajustar la tasa de arena, se equilibran la humedad y la tasa de evaporación para evitar que el hormigón se seque y se agriete y se reduzca el riesgo de colapso. 1.1.4 Establecimiento de una base de datos de calidad empresarial
Al diseñar las proporciones del hormigón, la primera tarea es llevar a cabo el diseño y el cálculo, y seleccionar los parámetros en función de la diversa información disponible, sobre la base del sistema teórico y la experiencia en especificaciones. Es necesario establecer una base de datos de calidad empresarial.
1.2 Selección de parámetros clave
1.2.1 Base para la selección de parámetros basada en
Al determinar la cantidad de agua utilizada, se puede ajustar de acuerdo con el tipo de arena utilizada. La arena fina puede aumentar el consumo de agua de 5 a 10 kg/m3 de hormigón, mientras que la arena gruesa puede disminuir el consumo de agua de 5 a 10 kg/m3 de hormigón. Para un hormigón más fluido, primero mida el consumo de agua real necesario para un asentamiento de 90 mm como parámetro base y aumente gradualmente el consumo de agua con el aumento del asentamiento; por lo general, se requieren 5 kg de consumo de agua por cada 20 mm de asentamiento. Al elegir la tasa de arena, es necesario consultar las regulaciones: la arena fina necesita reducir la tasa de arena, mientras que la arena gruesa puede aumentar adecuadamente la tasa de arena y, para la construcción de paredes delgadas, elija una tasa de arena mayor.
1.2.2 Análisis de factores sensibles
En la preparación del hormigón, si la calidad de las materias primas cambia, es necesario analizar su posible impacto en el rendimiento del hormigón. El análisis de regresión se utiliza para aclarar la relación entre los parámetros y los valores característicos. Si no es posible establecer una relación funcional clara, la relación entre los dos se puede entender a través de la lista de datos.
1.2.3 Ajuste de la selección de parámetros
El ajuste de la selección de parámetros debe combinarse con la experiencia y ajustarse acumulando una gran cantidad de datos. Al mismo tiempo, puede considerarse como un ajuste de tendencia, que calcula con precisión la posible influencia del rendimiento del hormigón según el cambio de parámetro, a fin de eliminar la influencia de los posibles cambios de factores.
Además, los ajustes de selección de parámetros son ajustes subjetivos y el efecto de un factor se puede analizar cuantitativamente. Los resultados de la mezcla de prueba deben usarse para la verificación para determinar la selección final de parámetros.
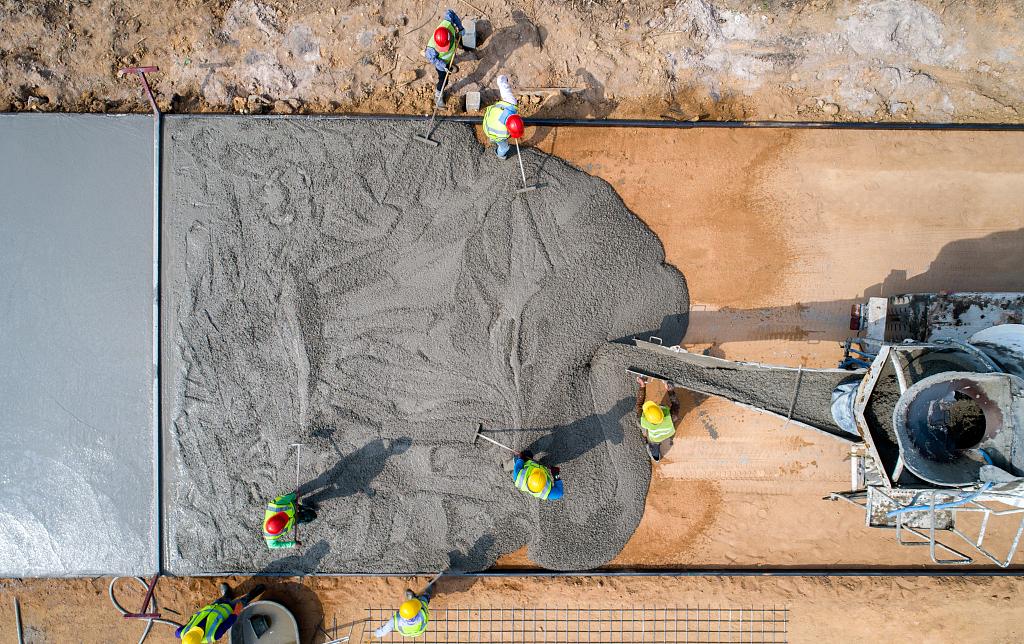
2.Emparejamiento de pruebas
2.1 Selección de materias primas de ingeniería reales
2.1.1 Muestreo representativo
En la pila de muestreo de materiales, afectada por una variedad de factores, como el tamaño de la pila, la dirección, el entorno, etc., es necesario transportarlos a través del proceso de muestreo continuo y equilibrado para obtener los materiales necesarios para la mezcla de prueba.
2.1.2 Toma de muestras
En el proceso de toma de muestras, asegúrese de que la muestra sea una representación verdadera de la materia prima y, al mismo tiempo, tenga un alto grado de homogeneidad. El método de cuadratura se utiliza a menudo como método de muestreo común.
2.1.3 Recopilación de datos
En primer lugar, recopile todos los informes de inspección de las materias primas en el trabajo diario.
En segundo lugar, establezca una base de datos especial para los informes de inspección de materias primas, combínelos con los resultados de las pruebas de las estadísticas y analice los informes de inspección de varios proveedores para determinar su precisión. Si el informe de inspección de un proveedor es más preciso en un período de tiempo más largo, se puede aplicar directamente en el diseño de la proporción de hormigón.
En el transcurso del trabajo, es necesario recopilar cada informe de inspección e informe de prueba de los proveedores de materias primas. Para el suministro de cemento en punto fijo, comprenda con precisión el patrón de crecimiento real de la resistencia del cemento y aplique el método de análisis de regresión para deducir la resistencia del cemento a los 28 días.
2.2 Método de mezcla durante la mezcla de prueba
El hormigón premezclado generalmente se mezcla utilizando el método de adición de agua y el método de alimentación separada. Dado que el hormigón premezclado a menudo adopta diferentes métodos de mezcla, es necesario conocer el método de mezcla adoptado por su propia estación de mezcla durante el proceso de mezcla de prueba y formular un método de mezcla adecuado para la mezcla de prueba sobre esta base.
2.3 Prueba de rendimiento y resistencia del hormigón
En primer lugar, después de determinar la proporción de mezcla del hormigón, el hormigón se mezcla estrictamente de acuerdo con los parámetros. Pruebe el asentamiento y la trabajabilidad reales del hormigón. Si la trabajabilidad y el asentamiento no cumplen con el estándar, es necesario fijar la proporción agua-cemento y ajustar constantemente la tasa y la cantidad de arena hasta que cumpla con los requisitos para obtener la proporción de mezcla de referencia.
Generalmente se utilizan más de tres proporciones diferentes para la prueba de resistencia del hormigón, una de las cuales se utiliza como la proporción de referencia, respectivamente aumentar y disminuir 0,05 como las otras dos proporciones, con el consumo de agua de la proporción de referencia, aumentar y disminuir 1% de la tasa de arena.
Si las condiciones lo permiten, se requiere lo siguiente para seleccionar el número de conjuntos de bloques de prueba de mezcla de prueba de resistencia:
a. Cuente las tasas de crecimiento de la resistencia de 3 y 7 días junto con la resistencia de 28 días.
b. Calcule la desviación estándar y el coeficiente de variación de la resistencia para las resistencias de 3, 7 y 28 días.
c. Utilice la resistencia de 3 días para derivar la resistencia de 28 días.
d. Determine la resistencia de los resultados de la mezcla de prueba.
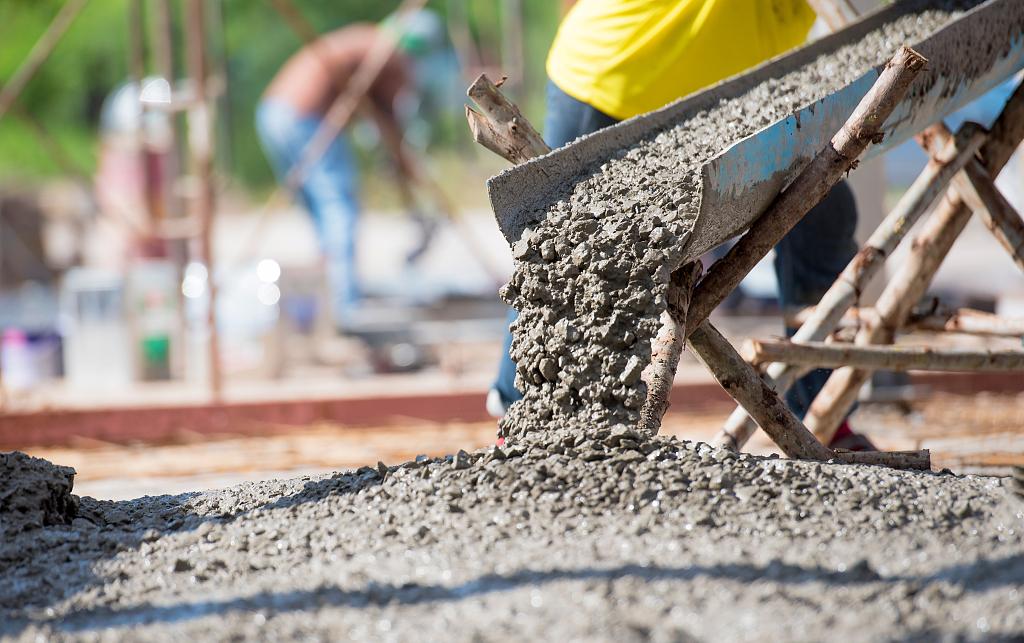
3. Ajuste de la proporción de hormigón tras la mezcla de prueba
En primer lugar, se comprueba la trabajabilidad y el asentamiento del hormigón de prueba y se determina el consumo de agua de acuerdo con el resultado de la comprobación.
En segundo lugar, se determina el tiempo de fraguado real del hormigón de prueba y se comprueba su trabajabilidad al mismo tiempo. Sobre esta base, se determina la cantidad óptima de aditivos añadidos y la tasa de arena más adecuada. Si la retención de agua del hormigón es deficiente y el tiempo de fraguado es demasiado largo, es necesario controlar eficazmente la adición de aditivos y aumentar moderadamente la tasa de arena. Si la consistencia del hormigón es alta y la pérdida de asentamiento es grande, es necesario aumentar moderadamente la cantidad de aditivo añadido o reducir moderadamente la tasa de arena. En el proceso de ajuste de los aditivos, se debe tener en cuenta que el efecto de reducción de agua puede verse afectado, por lo que también es necesario ajustar la relación agua-cemento y el consumo de agua.
En tercer lugar, la relación agua-cemento del hormigón se determina mediante los resultados de la prueba de resistencia del hormigón, que a su vez determina la cantidad de material de gel. Si se determina que la resistencia del hormigón es demasiado alta, se puede aumentar la relación agua-cemento de forma adecuada. Si la tarea de producción es apretada, solo se puede probar la resistencia del hormigón a los 3 o 7 días, a fin de deducir la resistencia a los 28 días, y la relación agua-cemento se puede ajustar de forma adecuada sobre esta base. Calcule la cantidad de agregados gruesos y finos en función del peso de capacidad del hormigón medido y la tasa de arena determinada en la mezcla de prueba.