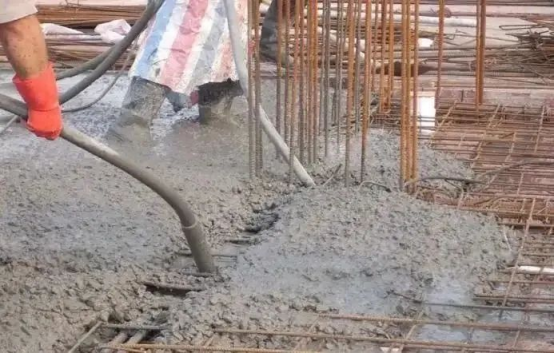
1. Materias primas
El módulo de finura y el contenido de limo de la arena deben cumplir los requisitos, y el contenido de agua no debe superar el 6 % durante el uso. El muestreo de arena no debe tomar la capa superficial y las partículas de gran tamaño de la grava superior, etc. deben cumplir los requisitos, especialmente el contenido de limo (contenido de polvo de piedra). Si no se cumplen los requisitos, la gradación de partículas de la grava debe ser básicamente uniforme, el agente reductor de agua continuo y el agente incorporador de aire deben haber pasado la inspección, y el tiempo de almacenamiento no debe superar los 6 meses. Se ha comprobado la resistencia del cemento a los 3 días y se ha determinado que cumple los requisitos del contrato, y se han realizado pruebas a las cenizas volantes y se ha determinado que cumplen los requisitos.
2.Proporción de la mezcla de construcción
La proporción de mezcla aprobada se utilizará como base para el ajuste de acuerdo con el módulo de finura y el contenido de agua de la arena y el contenido de agua de la grava. No se añadirá agua durante la construcción, pero la cantidad de agente reductor de agua puede ajustarse en un pequeño rango de acuerdo con la trabajabilidad. Cuando llueva, si aumenta el contenido de agua de la arena y la grava (debido a la falta de protección contra la lluvia de la tolva y el silo, o a un aumento del contenido de agua durante la carga, etc.), la cantidad de agua utilizada en la proporción de mezcla de construcción se reducirá en comparación con la cantidad utilizada antes de la lluvia, y no se realizarán otros ajustes a la ligera.
3. Detección y ajuste del asentamiento Al mezclar los dos primeros lotes, se debe verificar el asentamiento y la trabajabilidad de cada lote de hormigón en la salida. Normalmente, el asentamiento se prueba en el lugar de vertido. La cantidad de agua utilizada en la proporción de mezcla de construcción se reducirá en comparación con la cantidad utilizada antes de la lluvia, y no se realizarán otros ajustes a la ligera.
3.Detección y ajuste del asentamiento
Al mezclar los dos primeros lotes, se debe comprobar el asentamiento y la trabajabilidad de cada lote de hormigón a la salida de la máquina. Normalmente, el asentamiento se comprueba en el lugar de vertido. La cantidad de reductor de agua se puede ajustar adecuadamente según el asentamiento. Los requisitos de detección del asentamiento se llevarán a cabo de acuerdo con los procedimientos operativos prescritos.
4.Tratamiento de juntas de construcción
Se debe extender un mortero con una relación agua-cemento de 0,03-0,05 inferior a la del hormigón, pero no inferior a la del mismo grado, sobre la junta de construcción con un espesor de 2-3 cm. El área de extensión debe ser apropiada para la velocidad de vertido. La junta de construcción debe estar húmeda antes de extender el mortero. El cincelado de las juntas de construcción debe cumplir los requisitos y limpiarse para eliminar cualquier residuo. Debe aplicarse una capa de lechada de cemento (relación agua-cemento 0,03-0,05 inferior a la del hormigón) a las juntas verticales, y el área de aplicación debe ser adecuada a la velocidad de vertido.
5.Entrada en el silo
La altura del hormigón en el silo no debe ser superior a 2 m. Si se utiliza un distribuidor para introducir el hormigón en el silo, la distancia entre los tubos de la tolva debe ser de 2,5-3,0 m. El hormigón debe introducirse en el silo de forma secuencial, colocando primero la primera capa y luego las siguientes. Sin embargo, todo el hormigón debe cubrirse y vibrarse antes de que fragüe. Debe retirarse cualquier hormigón de calidad inferior que ya se haya colocado en el silo. El ángulo de la cinta transportadora no debe superar los 6 grados. La cinta transportadora y los tubos de la tolva deben mantenerse húmedos.
6. Nivelación del almacén
El almacén debe nivelarse a tiempo y no debe permitirse que se acumule el material en su interior. Al nivelar el almacén manualmente, el espesor de la capa debe ser de 30-50 cm (pseudo-colocación), y no debe exceder 1,25 veces la altura del vibrador. Al descargar, el agregado concentrado debe distribuirse manualmente de manera uniforme en los lugares con más mortero, y el agua de purga debe eliminarse a tiempo sin quitar la lechada de cemento. Si la parte inferior de la losa del suelo no se puede nivelar manualmente debido a limitaciones como barras de acero, una persona especial debe dirigir al distribuidor para que entre en el silo, controlar la parte de entrada de hormigón y la cantidad de hormigón que entra en el silo, y asegurarse de que el hormigón no sea demasiado espeso para evitar el fenómeno de concentración de agregados. La superficie de hormigón de la losa del suelo o la superficie superior de la losa superior debe nivelarse manualmente, y la superficie del silo debe estar aproximadamente nivelada y ligeramente más alta que la elevación diseñada antes de que se haga vibrar el vibrador de la losa.
7. Vibración del hormigón
debe vibrar primero el área cercana al encofrado (teniendo cuidado de no golpearlo) e insertarlo unos 5 cm en la capa inferior de hormigón. Los puntos de vibración deben tener forma de flor de ciruelo, con una separación no superior a 1,5 veces el rango efectivo de vibración. Insertar rápidamente y tirar lentamente para evitar chapoteos y burbujas. El rango efectivo de vibración se determina generalmente mediante pruebas. Por lo general, la superficie vertical de hormigón se inserta en el hormigón y se vibra sucesivamente. Si está ligeramente inclinada, la dirección de inclinación de cada punto de inserción debe ser la misma para evitar vibraciones perdidas. El tiempo de vibración habitual es de 15-20 segundos. Debido a las diferencias en el asentamiento y la trabajabilidad, el tiempo de vibración varía mucho. El tiempo de vibración para cada valor se basa en cuando el hormigón no se hunde significativamente, no aparecen burbujas y el hormigón comienza a asentarse. La primera capa de hormigón vertida o el área de unión de dos descargas debe vibrarse más intensamente. La placa inferior o superior generalmente necesita un vibrador de placa para la vibración de la superficie, y la superficie debe aplanarse manualmente. El grosor de vibración del vibrador de losas es pequeño. Si el material de pavimentación supera los 15-20 cm, es necesario vibrar con una varilla vibradora y luego con un vibrador de losas. Los requisitos para vibrar con una varilla vibradora son los mismos que los anteriores. Es decir, la velocidad de movimiento del vibrador de losas debe acelerarse adecuadamente.
8. Vibrar el hormigón cerca del waterstop
Se debe tener especial cuidado al vibrar alrededor del waterstop. La varilla vibradora no debe tocar el waterstop. Al colocar el hormigón debajo de la junta de agua horizontal, alguien debe levantar primero la junta de agua manualmente y luego colocarla sobre la superficie del hormigón vibrado después de la vibración. Al colocar el hormigón encima de la junta de agua, no debe tocar la junta de agua. Debe controlarse para que esté al menos a unos 50 mm de distancia de la junta de agua, y también debe asegurarse de que el área alrededor de la junta de agua se vibre densamente. Cuando el vibrador no pueda vibrar densamente, se debe utilizar una vibración manual suplementaria.
9. Inspección de las superficies de las capas intermedias y control del tiempo de vertido del hormigón
Las capas se construirán en la secuencia de vertido determinada en el plan de construcción, y el espesor de la capa deberá cumplir los requisitos. La longitud de cada capa será coherente con el plan. Se registrará el tiempo de vertido de cada parte de cada capa para recordar a la unidad de construcción que debe cubrir la capa superior y pasar a la siguiente capa antes de que fragüe el hormigón de esa parte. Si se comprueba que la unidad de construcción tarda demasiado en cubrir el hormigón antes de que fragüe, se le impedirá seguir vertiendo hormigón. El vertido de hormigón debe ser continuo. Si se excede el tiempo de intervalo (el tiempo de fraguado inicial), la capa superior de hormigón no debe cubrirse y debe tratarse como una junta de construcción. El tiempo de intervalo no debe exceder el tiempo de fraguado inicial. Este tiempo es el tiempo desde la descarga del hormigón desde la salida hasta la finalización de la cobertura de la capa superior de hormigón y la vibración. Cuando el hormigón pueda remodelarse, la construcción puede continuar. (El vibrador vibra durante 30 segundos, sin agujeros y con hormigón fresco a menos de 10 cm de la superficie).
El tiempo de intervalo depende de la temperatura y el cemento utilizados al verter el hormigón. Debido a las diferencias entre las condiciones del lugar y las condiciones del laboratorio, el tiempo de fraguado inicial del hormigón medido en el laboratorio no puede utilizarse para controlar el proceso de vertido.
10. Evaluación del fraguado inicial
A juzgar por la apariencia: Si se golpea el hormigón con una pala varias veces, no hay signos de sangrado o ablandamiento, o se forma una piel, o el hormigón ya no salpica (en un rango de 10 cm) cuando se vibra, hay agujeros después de retirar el vibrador, o hay ligeras marcas cuando se presiona con el dedo, etc., entonces puede que se haya fraguado. A juzgar por el tiempo: Si se ha dejado fraguar durante demasiado tiempo, puede que se haya fraguado. Esto está relacionado con el clima, etc., y no es muy preciso. La prueba de laboratorio es más precisa, pero no se puede utilizar para determinar el tiempo de fraguado durante la construcción in situ.
11. Inspección del encofrado
Durante el proceso de vertido del hormigón, se debe revisar y ajustar con frecuencia la forma y la posición del encofrado. Si el encofrado está deformado, se debe instruir inmediatamente a la unidad de construcción para que tome medidas efectivas para rectificarlo; de lo contrario, se debe ordenar que se detenga el vertido del hormigón. Cualquier fuga debe ser bloqueada inmediatamente. Para evitar las raíces del hormigón, la estanqueidad de las esquinas inferiores es particularmente importante. (Se debe controlar la estanqueidad del molde cuando se erige, se debe bloquear el exterior del molde con mortero, etc., y el mortero en la junta de construcción durante el vertido se puede espesar intencionadamente de forma adecuada en las esquinas, pero no debe ser superior a 5 cm. Durante la inspección del almacén, se debe verificar la uniformidad del encofrado, la estanqueidad y firmeza de las juntas. También se debe bloquear el espacio entre el refuerzo y el encofrado, y se deben sellar las juntas entre el encofrado con cinta adhesiva de doble cara.
12. Restablecimiento y unión del refuerzo
Teniendo en cuenta las necesidades de la construcción, es posible que haya que mover algunas barras de refuerzo durante el proceso de construcción, pero se debe prestar atención a la reposición y el atado oportunos.
13. Enlucido de hormigón
Si es necesario alisar con llana, se debe supervisar a la unidad de construcción para que lleve a cabo el alisado con llana y el alisado en general de manera oportuna. El alisado con llana generalmente debe llevarse a cabo en tres etapas. La primera vez se realiza después de la vibración, generalmente con una llana de madera, y la superficie grande debe nivelarse, con la uniformidad que cumpla con los requisitos. La segunda vez se realiza antes del fraguado inicial, generalmente con una llana de hierro, y la tercera vez se realiza durante el fraguado inicial, también con una llana de hierro (alisado). Se debe tener cuidado de no perturbar el hormigón cuando se alise con llana por segunda vez.
14. Momento de cincelar
La superficie de la junta de construcción debe rugosearse con agua a alta presión. Si la superficie de la junta de construcción ha estado en contacto con el hormigón durante demasiado tiempo, debe rugosearse con una chorreadora de arena neumática. Si es necesario, la superficie de la junta de construcción puede rugosearse manualmente para eliminar todo el hormigón flotante, el material suelto y los contaminantes. La superficie rugosa debe revelar arena gruesa o piedras pequeñas, pero no debe dañar el agregado interno. El cincelado de la junta de construcción debe realizarse después de que el hormigón haya ganado resistencia, que generalmente no es inferior a 5 MPa. No debe hacerse demasiado pronto, y generalmente se lleva a cabo al segundo día después del vertido, con un retraso apropiado en la temporada de bajas temperaturas.
15. Mantenimiento
Después de verter el hormigón, debe cubrirse y rociarse con agua lo antes posible una vez recogida la lechada. Esto suele hacerse durante 12-18 horas, y el tiempo debe adelantarse en la temporada de altas temperaturas. La superficie de hormigón no debe dañarse ni contaminarse durante la cobertura. Cuando la superficie de hormigón se cubra con un encofrado, este debe mantenerse húmedo con frecuencia durante el período de curado.
Cuando la temperatura sea inferior a 5 ℃, el encofrado debe cubrirse con aislamiento y no debe rociarse agua sobre la superficie de hormigón. Los requisitos para el agua utilizada para curar el hormigón son los mismos que para el agua de amasado.
La duración del rociado para el curado del hormigón se especifica en los términos técnicos del contrato y puede ampliarse o acortarse según corresponda, dependiendo de la humedad del aire, la temperatura, el tipo de cemento y los aditivos utilizados. Durante el período de curado, el número de rociados por día debe ser suficiente para mantener la superficie de hormigón constantemente húmeda.
Cuando la estructura entre en contacto con agua superficial o subterránea, deben tomarse medidas de impermeabilización y drenaje para garantizar que el hormigón no sea arrastrado por el agua en los 7 días posteriores al vertido. Cuando el agua circundante tenga un efecto erosivo, el hormigón debe protegerse de la inmersión en agua hasta que alcance el 70 % de la resistencia prevista en un plazo de 10 días. El hormigón no debe someterse a cargas de peatones, vehículos, encofrados, andamios u otras estructuras hasta que alcance una resistencia de 2,5 MPa. Si se requiere un curado al vapor, debe llevarse a cabo de acuerdo con los requisitos pertinentes de este capítulo, y debe completarse oportunamente un registro de inspección del curado al vapor.
16. Inspección de desencofrado
Después de verter el hormigón, la unidad de construcción deberá presentar una solicitud para retirar el encofrado, y el encofrado solo se retirará colectivamente si se cumplen los requisitos. La unidad de construcción deberá presentar un informe de resistencia de los bloques de prueba de hormigón que se hayan curado en las mismas condiciones, y el encofrado solo se retirará si se cumplen los requisitos. Cuando se retire el encofrado, se inspeccionará in situ la situación tras su retirada, incluyendo panales, superficies picadas, plataformas incorrectas, grietas, etc. No se permitirá a la unidad de construcción manchar o encubrir arbitrariamente diversos problemas de calidad o defectos en el hormigón. Cualquier problema o defecto de calidad importante deberá ser reportado de manera oportuna. Preste atención a la inspección frecuente del hormigón en busca de grietas, inste a la unidad de construcción a que haga buenos registros de observación y compruebe con frecuencia los registros de observación.
17. Procedimientos de gestión de defectos de calidad
Si se encuentra un defecto de calidad durante la inspección, la unidad de construcción y la unidad supervisora deberán elaborar rápidamente registros de inspección y encontrar la causa. La unidad supervisora revisará y aprobará el plan de gestión de defectos de acuerdo con su autoridad, y permanecerá atenta durante la gestión de defectos para supervisar la construcción de la unidad de construcción de acuerdo con el plan aprobado, rellenando rápidamente los registros de supervisión.
Para los defectos de categoría I, se llevarán registros antes de que se traten los defectos, se realizarán inspecciones antes de que se traten los defectos y se realizarán inspecciones de aceptación después de que se traten los defectos. Para los defectos de categoría II, se realizarán inspecciones conjuntas antes de que se traten los defectos y se realizarán inspecciones de aceptación conjuntas después de que se traten los defectos. Si es necesario, se invitará a expertos pertinentes a revisar el plan de tratamiento de defectos.