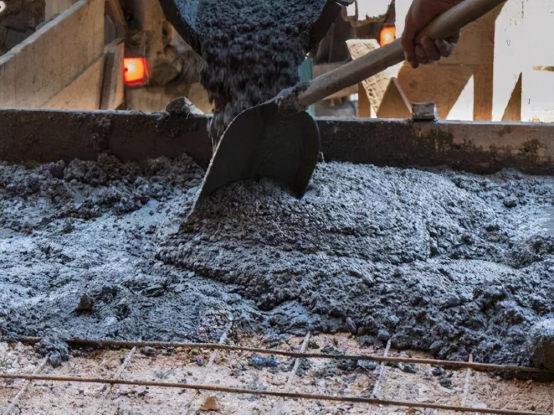
Hoy en día, el hormigón comercial se utiliza ampliamente. La trabajabilidad, durabilidad, resistencia y otros indicadores del hormigón han mejorado enormemente bajo el control de las plantas de mezcla. Sin embargo, debido a la distancia de transporte, las variedades de cemento, los aditivos y otras razones, el tiempo de fraguado anormal del hormigón comercial se ha convertido en una preocupación creciente.
1 Tiempo de fraguado del hormigón
Después de añadir agua al hormigón comercial, el cemento se hidrata y, con el tiempo, la lechada pierde gradualmente su liquidez y plasticidad. Este proceso se denomina fraguado del hormigón. El tiempo de fraguado inicial es el tiempo que transcurre desde que el cemento se mezcla con agua hasta que la lechada comienza a perder su plasticidad. El tiempo de fraguado final es el tiempo que transcurre desde que el cemento se mezcla con agua hasta que la lechada pierde completamente su plasticidad y comienza a desarrollar resistencia.
2 Tipos de fraguado anormal del hormigón
El fraguado anormal del hormigón suele manifestarse de tres maneras: fraguado lento, fraguado rápido y seudofraguado. El fraguado rápido y el seudofraguado pueden dificultar el hormigonado. El fraguado lento puede provocar un desmolde prolongado, una baja resistencia inicial y, en casos graves, una resistencia a los 28 días que no cumple los requisitos de diseño, lo que da lugar a un incidente de calidad.
3 Análisis de las causas y los riesgos de un fraguado anormal del hormigón
3.1 Fraguado rápido y seudofraguado
El fraguado rápido se caracteriza por el hecho de que, después de que el cemento entra en contacto con el agua, la lechada fragua rápidamente para formar una mezcla muy gruesa con poca trabajabilidad, y fragua rápidamente con una gran cantidad de liberación de calor. El seudofraguado se caracteriza por el hecho de que, después de que el cemento entra en contacto con el agua, fragua en pocos minutos sin un aumento significativo de la temperatura. Si se vuelve a mezclar en este punto, aún puede recuperar la plasticidad y utilizarse para verter y fraguar en su forma habitual.
Hay varias razones principales para esto:
En primer lugar, el proceso de calcinación del horno de cemento no es suficiente o incluso, y el clínker contiene clínker reducido.
En segundo lugar, el cemento contiene muchos álcalis, y el carbonato alcalino puede reaccionar con el Ca(OH)2 en el cemento para precipitar el CaCO3. La formación de este carbonato cementoso acelera el fraguado del cemento.
En tercer lugar, el uso inadecuado de cemento de resistencia temprana (cemento marcado con una R) también puede causar un fraguado rápido del hormigón.
En cuarto lugar, cuando se utilizan aditivos como lignosulfonato de calcio, sulfoaluminato de calcio, hidroxialquilaminas policarboxílicas y compuestos orgánicos que contienen ácidos hidroxicarboxílicos, o aditivos compuestos que contienen estos ingredientes, puede producirse un fraguado rápido debido a la incompatibilidad entre el aditivo y el cemento.
En quinto lugar, el fraguado rápido también puede producirse cuando la temperatura ambiente durante el mezclado del hormigón es superior a 35 °C y la temperatura del hormigón a la salida de la mezcladora es superior a 35 °C.
3.2 Fraguado retardado
La ingeniería de la construcción requiere que el tiempo de fraguado final del hormigón sea generalmente de unas 10 a 14 horas (excepto para el hormigón con requisitos especiales). El fraguado retardado se produce cuando el tiempo de fraguado final del hormigón supera considerablemente el tiempo de fraguado diseñado o esperado. También hay varias razones principales para esto:
En primer lugar, el tiempo de fraguado del cemento es demasiado largo. El fraguado del hormigón se debe principalmente al fraguado del cemento, por lo que el tiempo de fraguado del cemento determina la duración del tiempo de fraguado del hormigón.
En segundo lugar, las cantidades excesivas de retardadores o reductores de agua retardantes son la principal causa de los largos tiempos de fraguado del hormigón o incluso de la falta de fraguado durante varios días.
En tercer lugar, cuando la calidad o la cantidad de aditivos (cenizas volantes, polvo mineral, etc.) no es la adecuada, es probable que se produzca un fraguado anormal. Las cantidades excesivas pueden provocar un retraso en el fraguado.
En cuarto lugar, la incompatibilidad entre los reductores de agua y el cemento y los aditivos.
En quinto lugar, las técnicas o medidas de construcción inadecuadas.
En sexto lugar, además de los factores anteriores. La baja temperatura ambiente, la baja actividad del material de mezcla (o aditivo mineral) y la gran cantidad de aditivo, así como el cemento demasiado grueso, también pueden prolongar el tiempo de fraguado del cemento.
Cuando el hormigón fragua lentamente, pueden surgir los siguientes peligros: En primer lugar, retrasos en el calendario de construcción, lo que puede hacer que los procesos posteriores no puedan desarrollarse con normalidad. En segundo lugar, el tiempo de fraguado final es demasiado largo, lo que da lugar a una mala calidad del hormigón. En tercer lugar, se produce una pérdida económica significativa.
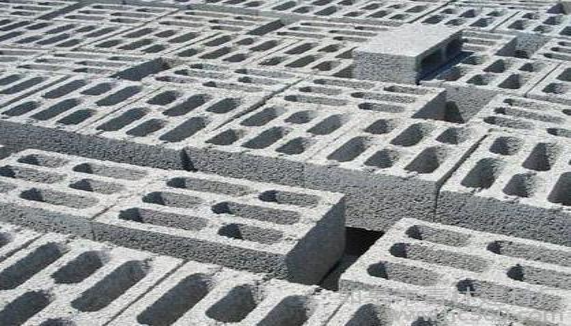
4 Prevención del fraguado anormal
4.1 Investigación de las materias primas producidas por la planta de materias primas
Al seleccionar las materias primas para la planta de mezclado, se debe realizar previamente un estudio de las materias primas producidas por la planta de materias primas. La inspección no debe ser una mera formalidad, y el precio no debe ser la única base para el juicio. Tomando como ejemplo las plantas de cemento, se deben realizar controles estrictos en cuanto a la escala de producción, la capacidad de producción, el nivel de proceso, el nivel de personal, la gestión de mediciones y otros aspectos. En particular, se debe garantizar que las plantas de cemento no puedan utilizar anhidrita, yeso semihidratado, yeso fosforado y otros materiales preparados para el cemento. Elija cemento con el tiempo de fraguado adecuado. Un cemento con un tiempo de fraguado largo es una causa importante del fraguado ultralento del hormigón. En términos generales, se debe preferir el cemento de horno rotatorio para producir hormigón premezclado, y se debe elegir cuidadosamente el cemento de horno vertical; se debe elegir cemento Portland y cemento Portland ordinario.
4.2 Aumentar la comunicación con los fabricantes de materias primas
Durante el proceso de producción del hormigón, debe aumentarse la comunicación con los fabricantes de materias primas. Cuando cambien los indicadores clave de las materias primas proporcionadas por los fabricantes de materias primas, como la tecnología de procesamiento y la proporción de mezcla de los componentes, debe comprenderse la situación de manera oportuna y deben tomarse medidas. Cuando cambie la estación y el fabricante, debe probarse la adaptabilidad del cemento, los aditivos y los materiales de mezcla. 4.3 Seleccionar correctamente los aditivos
En particular, evite la sobredosis de retardadores o reductores de agua de tipo retardador. La elección del retardador o del reductor de agua de tipo retardador debe determinarse caso por caso. Dado que algunos retardadores o reductores de agua de tipo retardador tienen un fuerte efecto retardante, la sobredosis puede provocar un retraso o incluso un no fraguado a largo plazo, por lo que la dosis debe ser precisa. Dado que la dosis es muy pequeña, es mejor utilizar un agente a base de agua o disolver el material sólido en agua antes de añadirlo.
4.4 Control del agua utilizada para mezclar el hormigón
Cuando el agua utilizada para mezclar el hormigón contiene sustancias como aceite, ácido, azúcar o cuando la cubierta de curado final contiene este tipo de sustancias, también puede provocar un fraguado anormal. Por esta razón, la normativa estipula que el agua de amasado utilizada en la planta de mezclado debe ser agua que haya superado las pruebas requeridas.
4.5 Gestión estricta de las mediciones de la planta de mezclado
Se debe nombrar a un metrólogo y encargar a la oficina de metrología local (distrital o municipal) que realice controles de calibración de la hormigonera y otros equipos de producción y prueba. La planta de mezcla debe organizar y archivar el informe de confirmación del control de calibración. El metrólogo debe realizar el muestreo, la reparación y el mantenimiento de los equipos de producción y prueba. El personal sin licencia no puede utilizar los equipos, y el uso y funcionamiento de los mismos debe seguir estrictamente los procedimientos y normas. Esto evitará problemas con el hormigón causados por problemas de medición con el equipo.
4.6 Gestión estricta de la cámara de pruebas de la planta de mezcla
El laboratorio es una parte importante del control de calidad en la planta de mezclado. El tiempo de fraguado del hormigón puede determinarse mediante la resistencia a la penetración de 3,5 MPa y 28 MPa. Por lo tanto, el laboratorio de la planta de mezclado es la forma más directa y eficaz de controlar el tiempo de fraguado del hormigón acabado. Siempre que haya un cambio estacional, un cambio en el proyecto o un cambio en las materias primas, el laboratorio debe ser el primero en informar del cambio en el tiempo de fraguado y ajustar la proporción de la mezcla.