
Después de usar mortero de cemento para enlucir, a menudo ocurren accidentes de calidad como grietas, huecos y caídas, lo que a su vez provoca grietas o caídas de la capa decorativa exterior sobre la capa de yeso, lo que afecta gravemente la calidad decorativa de la pared. El rendimiento del mortero de enlucido y la tecnología de construcción del enlucido son los principales factores que afectan la calidad de la capa de enlucido.
El mortero de yeso se usa ampliamente para nivelar la construcción antes de la decoración fina de las paredes. Sin embargo, la capa de yeso enlucida con mortero de cemento a menudo sufre accidentes de calidad como grietas, huecos y caídas, lo que a su vez hace que la capa decorativa exterior sobre la capa de yeso se agriete o se caiga, afectando gravemente la calidad decorativa de la pared. . El mortero se contrae debido a la pérdida de agua, y la contracción es grande en la superficie y pequeña en el interior, lo que hace que la capa de yeso se deforme hacia afuera y se separe de la capa base, ahuecando y eventualmente cayendo al mismo tiempo. si el tratamiento de la capa base y las técnicas de construcción del enlucido son inadecuadas, también provocará la contracción del mortero. Por lo tanto, reducir la contracción del mortero y restringir los requisitos de construcción del enlucido puede controlar eficazmente los problemas de calidad de la capa de yeso.
1. Materias primas y pruebas.
Cemento: cemento de escoria con grado de resistencia 32,5;
Arena artificial: Zona I arena media con módulo de finura de 2,6, en la que w (polvo de piedra) es 6,40%;
Cenizas volantes: Cenizas volantes de grado 1, la proporción de demanda de agua es del 99%;
Pasta de cal: elaborada a partir de cal viva ordinaria molida con bolas y de consistencia 58 mm;
Masilla: Masilla resistente al agua.
2.Resultados de la prueba
2.1 Consumo de agua al alcanzar la consistencia especificada Con carácter general, cuanto mayor sea el consumo de agua del mortero al alcanzar la misma consistencia, mayor será la retracción correspondiente del mortero.
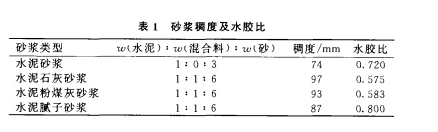
2.2 Prueba de resistencia a la compresión del cubo
La resistencia del mortero en condiciones de curado estándar es mayor que en condiciones de curado natural; la resistencia del mortero después de mezclarlo con mezclas es menor que la del mortero de cemento, por lo que el mortero mezclado con mezclas es más adecuado para su uso con niveles de resistencia más bajos. Construcción de muros livianos.
2.3 Prueba de tecnología de enlucido con mortero
En el exterior se construyeron dos muros con bloques huecos de hormigón ceramsita y ladrillos porosos sinterizados, se separaron y se realizaron ensayos de enlucido con cuatro morteros diferentes. Durante la construcción de enlucido, se realizan pruebas principalmente sobre el grado de humectación de la pared base y el intervalo de tiempo de enlucido entre la capa superficial y el mortero inferior. El grado de humectación de la pared de base se divide en: humectación completa (es decir, riego abundante, la tasa de absorción de agua de la pared está cerca del estado de saturación de absorción de agua) y estado de humectación incompleta. El intervalo de tiempo entre la capa inferior y la capa superficial de enlucido se determina como el inicio del fraguado final del mortero y 1 hora después del inicio del fraguado final (es decir, el grado de fraguado final alcanza del 70 al 80%, y en este momento, no quedarán marcas en la superficie de la capa de yeso con los dedos). El espesor de la capa inferior de mortero se controla entre 6 y 7 mm, y el espesor de la capa superficial de mortero se controla entre 8 y 9 mm. 24 horas después de completar el trabajo de enlucido, la capa de enlucido se debe rociar con agua para mantenimiento dos veces al día. Cada vez que se riega, se debe humedecer la superficie de enlucido y el riego se debe continuar durante 7 días. A continuación, la superficie enlucida de la pared se curó de forma natural al aire libre. Durante el mes de observación experimental, la temperatura ambiente exterior estuvo entre 16 y 26 ° C; la humedad estuvo entre 45 % y 70 % y hubo tres lluvias de ligeras a moderadas durante el período. Un mes después de finalizar la prueba de enlucido, se observó que salvo que el mortero de cemento no presentaba grietas importantes cuando estaba completamente mojado y después de un largo intervalo de tiempo, aparecían grietas en otros estados. Las capas de revoque de mortero de masilla de cemento y de mortero de cemento de cenizas volantes no presentaban grietas en ningún caso.
En caso de humedecimiento incompleto e intervalos de tiempo cortos, aparecerá una cantidad muy pequeña de grietas finas en la capa de revoque de mortero de cemento y cal, pero no aparecerán grietas en otras circunstancias.
3. Análisis y discusión de los resultados de las pruebas.
El agrietamiento de la capa de enlucido de mortero se debe principalmente a la contracción desigual causada por una gran pérdida de agua superficial y una pequeña contracción interna. Como resultado, la superficie del mortero soporta tensión y el interior soporta presión. Cuando la fuerza de tracción sobre la superficie del mortero excede su resistencia a la tracción, se producirán grietas. Por tanto, reducir el consumo de agua y aumentar la tenacidad del mortero son los principales métodos para controlar eficazmente la retracción del mortero. Parte del agua del mortero se utiliza para hidratar el material cementoso y la parte restante se utiliza para cumplir con los requisitos de consistencia. La mayor parte de este consumo de agua eventualmente se evaporará, lo que provocará que el mortero pierda agua y se contraiga. Por lo tanto, al preparar el mortero, bajo la premisa de cumplir con los requisitos de agua de hidratación y consistencia de la construcción, se debe reducir la relación agua-cemento tanto como sea posible para reducir el consumo de agua, lo que puede reducir la contracción causada por la pérdida de agua y controlar la aparición de grietas. Mezclar una cierta cantidad de cenizas volantes y cal en mortero de cemento puede reducir el consumo de agua y mantener la consistencia. Las cenizas volantes contienen grandes
La cantidad de perlas de vidrio hace que las cenizas volantes tengan una pequeña superficie interna específica y una pequeña demanda de agua. Tiene un efecto de retención de agua cuando se usa en mortero de cemento y también puede desempeñar un cierto efecto reductor de agua para reducir la contracción en seco debido. a la pérdida de agua. Además, las cenizas volantes también pueden mejorar la densidad del mortero, refinar los poros y rellenar los poros capilares dañinos. Cuando la cal viva se apaga en lechada de cal, puede formar automáticamente hidróxido de calcio con partículas extremadamente finas (aproximadamente 1 μm de diámetro) en un estado coloide disperso. Una película espesa de agua se adsorbe en la superficie y tiene buena plasticidad. Agregar mortero de cal al mortero de cemento puede mejorar la plasticidad, reducir el consumo de agua y reducir la contracción por secado. Cuando se incorpora masilla al mortero de cemento, se puede reducir la contracción sin ningún cambio en el consumo de agua. Esto se debe a que durante el proceso de coagulación y endurecimiento del mortero, el aglutinante de la masilla se seca formando una película en la zona de transición entre la arena y la lechada de cemento, haciendo que la unión entre ambos sea más densa y fuerte además, la masilla; Además de la arena, la otra parte se dispersará uniformemente en la lechada de cemento. En la etapa inicial de la hidratación del cemento, la masilla se adherirá al gel y a las partículas de cemento no hidratadas. , el agua en la lechada de cemento continuará Cuando se consume el gel y aumentan los hidratos, la masilla se acumulará en los poros capilares, formará una acumulación apretada en la superficie del gel y la superficie de partículas no hidratadas, y llenará gradualmente el poros capilares. A medida que la humedad de hidratación y secado disminuye aún más, el aglutinante de masilla acumulado en el gel y los poros se condensa en una película para formar una red de polímero, y el módulo elástico del polímero es menor que el del cemento, lo que reduce la tenacidad y tenacidad del Se ha mejorado la resistencia al agrietamiento del mortero de masilla, resistiendo eficazmente la contracción. Durante la construcción de enlucido, el propósito de mojar completamente la capa base es permitir que absorba suficiente agua y evitar
Evitar absorber humedad en el mortero de revoque y afectar la hidratación normal del mortero. El objetivo principal de controlar el intervalo entre el enlucido de la capa inferior y la capa superficial es garantizar que la capa inferior tenga una cierta resistencia y una cierta fuerza de unión. Si el intervalo es demasiado largo, el mortero de la capa inferior se endurecerá por completo, provocando que el mortero de la capa inferior se endurezca por completo. capa superficial de mortero a enlucir para formar una unión con la capa inferior 2 piezas de piel, no unidas firmemente, provocando grietas o caídas. Si el intervalo es demasiado corto, la capa inferior de mortero no ha alcanzado un cierto grado de condensación y quedará unida por el mortero recién aplicado y se caerá.
4.Conclusión
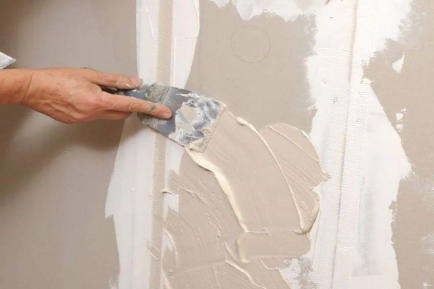
a. En materiales de pared con niveles bajos de resistencia, como bloques huecos de hormigón de ceramsita y ladrillos porosos sinterizados, el mortero de cemento con cenizas volantes, el mortero de masilla de cemento y el mortero de cemento y cal son adecuados para realizar capas de yeso cuando se utiliza mortero de cemento y cal. Después del enlucido, debe; Preste atención al control de las condiciones de mantenimiento. El enlucido con mortero de cemento puede reducir la aparición de grietas siempre que se garanticen técnicas de construcción adecuadas.
b. Agregar una cierta cantidad de mezclas (como cenizas volantes, pasta de cal, masilla, etc.) que puedan reducir el consumo de agua o mejorar la dureza del mortero en el mortero de cemento puede controlar eficazmente la aparición de grietas en la superficie del mortero. capa de yeso.
c. Durante la construcción del enlucido, la superficie de la pared base debe estar completamente humedecida; el intervalo entre la capa superficial y la capa inferior de enlucido no debe ser demasiado largo ni demasiado corto, y el fraguado final del mortero debe ser de 70 a 80 %.